Modbus Remote Control Butterfly Valve
Modbus Communication Protocol
Modbus is a serial communication protocol published by Modicon (now Schneider Electric) in 1979 for communication using programmable logic controllers (PLCs). Modbus has become the industry standard for industrial communication protocols (De facto) and is now the usual connection between industrial electronic devices.
Modbus allows multiple (approximately 240) devices to be connected to communicate on the same network, for example, a device that measures temperature and humidity and sends the results to a computer. In the Data Acquisition and Monitoring Control System (SCADA), Modbus is typically used to connect monitoring computers to remote terminal control systems (RTUs).
The Modbus protocol currently has versions for serial, Ethernet, and other networks that support Internet Protocol.
Most Modbus device communication takes place via the serial EIA-485 physical layer.
For serial connections, there are two variants that differ slightly in numerical data representation and protocol details. Modbus RTU is a compact, binary representation of data. Modbus ASCII is a human-readable, lengthy representation. Both variants use serial communication. Subsequent commands/data in the RTU format have a checksum of the cyclic redundancy check, while the ASCII format uses a checksum of the vertical redundancy check. Nodes configured as RTU variants will not communicate with nodes set to ASCII variants, and vice versa.
For connections over TCP/IP (such as Ethernet), there are multiple Modbus/TCP variants that do not require checksum calculations.
For all three communication protocols, the data model and function call are the same, only the package method is different.
Modbus has an extended version of Modbus Plus (Modbus+ or MB+), but this protocol is proprietary to Modicon and is different from Modbus. It requires a dedicated coprocessor to handle high-speed token rotation like HDLC. It uses 1 Mbit/s twisted pair and each node has a switching isolator, a device that uses a transition/edge trigger instead of a voltage/level trigger. Connecting Modbus Plus to a computer requires a special interface, usually a board that supports ISA (SA85), PCI or PMCIA bus.
The Modbus protocol is a master/slave architecture protocol. One node is the master node, and the other nodes that use the Modbus protocol to participate in communication are slave nodes. Every slave device has a unique address. In serial and MB+ networks, only nodes designated as master can initiate a command (on Ethernet, any device can send a Modbus command, but usually only one master device starts the command).
A ModBus command contains the Modbus address of the device that is intended to be executed. All devices will receive the command, but only the device at the specified location will execute and respond to the command (with the exception of address 0, the command specifying address 0 is a broadcast command, all devices that receive the command will run, but do not respond to the command). All Modbus commands contain check codes to determine that the command that was arrived is not corrupted. The basic ModBus command can instruct an RTU to change a value of its register, control or read an I/O port, and direct the device to return one or more of its registers.
There are many modems and gateways that support the Modbus protocol because the Modbus protocol is simple and easy to copy. Some of them are specially designed for this protocol. There are different implementations using wired, wireless communication and even short messages and GPRS. However, designers need to overcome some issues including high latency and timing.
fold
Almost all implementations are some variation of official standards. Communication between different vendor devices may not be possible. Some of the main changes are:
type of data
IEEE standard floating point number
32-bit integer
8-bit data
Mixed data type
Bit field in integer
Multipliers to change data to/from integer. 10, 100, 1000, 256 ...
Protocol extension
16-bit slave address
32-bit data size (1 address = return 32-bit data)
Word exchange data
Modbus was developed for programmable logic controller communication in late 1970. These limited data types were understandable by PLC at that time, and large binary object data was not supported.
For a node, there is no standard way to find the description of a data object. For example, determine if a register data represents a temperature between 30 and 175 degrees.
Since Modbus is a master/slave protocol, there is no way to require the device to "report anomalies" (built on top of the Ethernet TCP/IP protocol, except for open-mbus) - the master node must cycle through each node device, And look for changes in the data. In applications where bandwidth may be valuable, this approach consumes bandwidth and network time in the application, such as on low-rate wireless links.
Modbus can only handle 247 addresses on a single data link, which limits the number of devices that can be connected to the master site (except for Ethernet TCP/IP)
Modbus transmission is performed by buffering data between remote communication devices. There must be continuous restrictions on communication, which avoids the problem of buffer vulnerabilities in transmission.
The Modbus protocol itself provides no security for unauthorized commands or intercepting data.
Want Know More Please Watch The Video
Electric Butterfly Valve Show
Product Classification
FRYT—Part-Turn Electric Actuator 100NM-500NM Type
◆Sturdy construction, using dual-sealing, and can anti-water and dust(IP67/IP68-2m, 48 hours) effectively when filed connection.
◆Direct drive quarter-turn
◆Three phase, single phase and direct current power supply actuator
◆Multi-language text display screen displaying the state and setting
◆As the built-in data recording mechanism of the standard function
◆Compatible With IrDATM standard. Make the local and remote analysis on the actuator through insight PC software.
◆Concise, easy to control, and indication functions
◆Simple torque and position control, enhancing the reliability
◆Flexibility of comprehensive control and indication
◆Optional specification of water proof and explosion proof type
◆Direct torque output range 50Nm(37 Ibf ft)—500Nm(370 Ibf ft)
FRYT—Part-Turn Electric Actuator 1000NM-2000NM Type
◆Sturdy construction, using dual-sealing, and can anti-water and dust(IP67/IP68-2m, 48 hours) effectively when filed connection.
◆Direct drive quarter-turn
◆Three phase, single phase and direct current power supply actuator
◆Multi-language text display screen displaying the state and setting
◆As the built-in data recording mechanism of the standard function
◆Compatible With IrDATM standard. Make the local and remote analysis on the actuator through insight PC software.
◆Concise, easy to control, and indication functions
◆Simple torque and position control, enhancing the reliability
◆Flexibility of comprehensive control and indication
◆Optional specification of water proof and explosion proof type
◆Direct torque output range 600Nm(890 Ibf ft)—2000Nm(1476 Ibf ft)
Performance Data Of FRYT On-Off Type Actuator
Model | Revolving Speed (rpm) | Torque (Nm) | Voltage (V) | Phase (Ph) | Frequency (Hz) | Power (kW) | Rated Current (A) | Duty | Weight (kg) |
FRYT250 | 1 | 250 | 380 | 3 | 50 | 0.04 | 0.57 | S2(15min) | 23 |
FRYT500 | 0.5 | 500 | 380 | 3 | 50 | 0.04 | 0.57 | S2(15min) | 23 |
FRYT1000 | 1 | 1000 | 380 | 3 | 50 | 0.04 | 0.57 | S2(15min) | 37 |
FRYT2000 | 0.5 | 2000 | 380 | 3 | 50 | 0.04 | 0.57 | S2(15min) | 37 |
Performance Data Of FRYT Regulated Type Actuator
Model | Revolving Speed (rpm) | Torque (Nm) | Voltage (V) | Phase (Ph) | Frequency (Hz) | Power (kW) | Rated Current (A) | Duty | Weight (kg) |
FRYT250 | 1 | 250 | 380 | 3 | 50 | 0.04 | 0.57 | S4(30%) | 23 |
FRYT500 | 0.5 | 500 | 380 | 3 | 50 | 0.04 | 0.57 | S4(30%) | 23 |
FRYT1000 | 1 | 1000 | 380 | 3 | 50 | 0.04 | 0.57 | S4(30%) | 37 |
FRYT2000 | 0.5 | 2000 | 380 | 3 | 50 | 0.04 | 0.57 | S4(30%) | 37 |
Dimension Of FRYT Actuator (Direct Mounted)
Model | A | B | C | D | E | F | (G) | (H) | (I) |
FRYT1 | 306 | 124 | 160 | 135.5 | 202.5 | 277 | 430 | 338 | 54 |
FRYT2 | 308 | 121.5 | 160 | 123.5 | 245 | 340 | 428.5 | 368.5 | 52 |
Dimension Of FRYT Actuator (Foot-Plate Mounted)
Model | A1 | A2 | A3 | A4 | C | D1 | D | E | F | F1 | F2 | H1 | H2 | H3 | H4 | H5 | n-Φd1 | 4-Φd2 |
FRYT1 | 240 | 280 | 180 | 220 | 180 | 100 | 100 | 22 | 68.5 | 20 | 17.5 | 382 | 288 | 124 | 306 | 160 | 18 | 17.5 |
FRYT2 | 240 | 280 | 200 | 250 | 180 | 200 | 250 | 30 | 93 | 25 | 55 | 425 | 356 | 136 | 308 | 160 | 2-Φ20 | 22 |
Packaging
WOODEN CASE
After Sales Warranty
1 YEAR
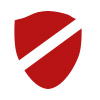
Sinopro Service Pledge
- Quality Product
- Order On-Line Tracking
- Timely Delivery
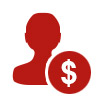
Sinopro Service Pledge
- Credit Rating
- Credit Services
- Credit Purchasing
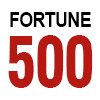
Sinopro Service Pledge
- 427+ Categories
- 2800+ Suppliers
- 200+ Brands