Seamless Casing 13 3/8'' 68PPF
Seamless casing accounts for the greatest amount of oil-field casing in use today. Each joint is manufactured in a pipe mill from a solid cylindrical piece of steel, called a billet. The billet is sized so that its volume is equal to that of the joint of pipe that will be made from it. The manufacturing process involves
• Heating the billet to a high temperature.
• Penetrating the solid billet through its length with a mandrel such that it forms a hollow cylinder.
• Sizing the hollow billet with rollers and internal mandrels.
• Heat treating the resulting tube.
• Final sizing and straightening.
The threads may be cut on the joints by the manufacturer or the plain-end tubes may be sent or sold to other companies for threading. The most difficult aspect of the manufacture of seamless casing is that of obtaining a uniform wall thickness. For obvious reasons, it is important that the inside of the pipe is concentric with the outside. Most steel companies today are very good at this. A small few are not, and that is one reason that API and ISO standards of quality were adopted. Current standards allow a 12.5% variation in wall thickness for seamless casing. The straightening process at the mill affects the strength of the casing. In some cases, it is done with rollers when the pipe is cool and other cases when the pipe is still hot. Seamless casing has its advantages and also a few disadvantages.
• Advantages of Seamless Casing.
• No seams to fail.
• No circumferential variation of physical properties.
• Disadvantages of Seamless Casing.
• Variations in wall thickness.
• More expensive and difficult manufacturing process.
Seamless casing accounts for the greatest amount of oil-field casing in use today. Each joint is manufactured in a pipe mill from a solid cylindrical piece of steel, called a billet. The billet is sized so that its volume is equal to that of the joint of pipe that will be made from it. The manufacturing process involves
• Heating the billet to a high temperature.
• Penetrating the solid billet through its length with a mandrel such that it forms a hollow cylinder.
• Sizing the hollow billet with rollers and internal mandrels.
• Heat treating the resulting tube.
• Final sizing and straightening.
The threads may be cut on the joints by the manufacturer or the plain-end tubes may be sent or sold to other companies for threading. The most difficult aspect of the manufacture of seamless casing is that of obtaining a uniform wall thickness. For obvious reasons, it is important that the inside of the pipe is concentric with the outside. Most steel companies today are very good at this. A small few are not, and that is one reason that API and ISO standards of quality were adopted. Current standards allow a 12.5% variation in wall thickness for seamless casing. The straightening process at the mill affects the strength of the casing. In some cases, it is done with rollers when the pipe is cool and other cases when the pipe is still hot. Seamless casing has its advantages and also a few disadvantages.
• Advantages of Seamless Casing.
• No seams to fail.
• No circumferential variation of physical properties.
• Disadvantages of Seamless Casing.
• Variations in wall thickness.
• More expensive and difficult manufacturing process.
Packaging
After Sales Warranty
Standard export package.
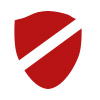
Sinopro Service Pledge
- Quality Product
- Order On-Line Tracking
- Timely Delivery
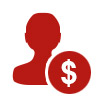
Sinopro Service Pledge
- Credit Rating
- Credit Services
- Credit Purchasing
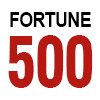
Sinopro Service Pledge
- 427+ Categories
- 2800+ Suppliers
- 200+ Brands